How to choose a good MOS tube?
The first step is to decide whether to adopt N channel or P channel MOS tube
In the use of vertical power, when a MOS tube is grounded and the load is connected to the feeder voltage, the MOS tube constitutes a high voltage side switch. In the high voltage side switch, the N channel MOS tube should be adopted for the consideration of the voltage required for the open or conductive parts. When the MOS tube is connected to the bus and the load is grounded, a low voltage side switch is used. The P-channel MOS tube is generally being adopted in a topology, also due to considerations of voltage drive.The additional voltage that must be required, or the maximum voltage allowed to be accepted by the machine. The higher the extra voltage, the higher the profit of the parts. According to the theoretical experience, the extra voltage should be greater than the feeder voltage or bus voltage. That capability requires the remaining cover so that the MOS tube does not take effect. In terms of MOS transistors, the maximum voltage acceptable between the drain electrode and the source electrode, namely the maximum VDS, must be determined. It is important to know that the maximum voltage acceptable to the MOS tube varies with the measurement. We need to test the voltage variation across the mission measurement spectrum. additional The voltage must have a residual margin to cover a transition area and ensure that the path does not take effect. Other elements of insurance that need to be considered include voltage transients induced by electrical appliances such as generators or transformers. There is no difference in the extra voltage used; Generally, the portable facilities are 20V, FPGA power supply is 20-30V and 85-220VAC is 450-600V. The KIA semi-superconductor's proposed MOS transistors work directly with high voltage and directly affect millions of millions of customers.
Affirm the additional DC current of the MOS tube
The additional DC shall be the maximum DC current that the load is acceptable under all conditions. Similar to the voltage condition, ensure that the selected MOS tube is capable of receiving an additional DC, even when a sporadic dc spike is occurring. The two contemplated DC conditions are sequential in form and pulse spikes. In the continuous on-off mode, the MOS tube is in steady state, and the DC current is passing through the parts one after another. A pulse spike is a small surge (or spike) of current through the machine. Once the maximum DC power in the agency's environment has been determined, an indirect choice can be made of the machine that can accept a given maximum DC power.
After selecting the additional DC current, it is necessary to plan the conduction consumption. In practice, MOS tube is not a real machine, because there will be kinetic energy consumption in the process of conducting heat, which is called conduction consumption. The MOS tube is "ON" like a variable resistor, as determined by the RDS (ON) of the device, and changes significantly with the measurement. The power loss of the components can be calculated by Iload2×RDS (ON), since the lead resistance changes with the measurement, the power loss will also change by comparison. The higher the voltage VGS applied to the MOS tube, the smaller the RDS (ON) will be. Conversely, RDS (ON) is going to be higher. Note that the RDS (ON) resistance will decrease slightly with dc. Changes in the electrical parameters of RDS (ON) resistors by nationality can be found in the list of skills and materials needed by the builder.
Choose MOS tube next step is piecemeal heat request
One must consider two dissimilar situations, the worst and the present. The proposed adoption of worst-case scenarios ensures that the bits do not go into effect because one outcome requires a larger margin of insurance. There are some measurement data that need to be noticed on the material table of MOS tube. The junction temperature of the machine is equal to the product of the maximum conditional measurement plus the thermal resistance times the power dissipation (junction temperature = the maximum conditional measurement + [thermal resistance × power dissipation]). According to a certain formula, the maximum power dissipation of fragments can be solved, that is, the definition is the same as I2×RDS (ON). We have to go through the maximum dc current of the machine and can plan out the RDS (ON) without the measurement. In addition, the channel plate and its MOS tube heat dissipation should be done well. Landslide breakdown means that the reverse voltage on the semi-superconductor parts exceeds the maximum value and constitutes a strong magnetic field to increase the direct current in the parts. The increase of chip size will improve the strength of wind collapse, and ultimately improve the stability of the machine. Thus, more selective packaging can be ineffective in preventing landslides.
The first step of choosing MOS tube is to decide on the switch function of MOS tube
There are many parameters for the function of reaction switch, but the most important are electrode/drain, electrode/source and drain/source storage capacity. The department's storage capacity will be in the machinery parts of the switch consumption, because they are in the previous switch to inflate. The MOS tube's switch progress is thus increased and the machine frequency is lowered. In order to calculate the total consumption of the parts in the switch process, the consumption in the opening process (Eon) and the consumption in the open process (Eoff) should be planned. The total power of MOSFET switch can be expressed as: Psw= (Eon+Eoff) × switch frequency. The electrode point charge (Qgd) has the greatest response to the function of the switch.
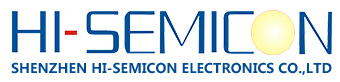