Recently, Taiwan media reported that due to the strong demand for 8-inch wafer OEM capacity, the delivery date has been extended to 4 months. Under the guidance of relevant guidance, wafer OEM factories in mainland China have started to operate at full capacity, giving priority to IC design companies in Mainland China to supply production capacity and reserve chip inventory in advance. In short supply, many IC designers have begun to advance the active price booking capacity, there are outgoing quotes will increase 10%.
Wafer contract price rise, also let some IC design factories decided to take the initiative to follow up the rise, in order to cope with rising OEM costs. Previously, strong demand for power management chips, panel driven IC and sensors, coupled with limited new production capacity on the wafer foundry line, had squeezed 8-inch wafer production capacity, and 8-inch foundries such as UmC and World Advanced were already full. MOS transistors, which also rely on 8-inch wafer capacity, have also been forced to adjust prices.
According to the report, the current MOSFET chip delivery cycle has been extended by one month, and products previously scheduled for normal delivery have been told to delay delivery. Many IC design industry insiders also revealed that due to limited 8-inch wafer OEM capacity constraints, the product delivery date has been extended from the past 2-3 months to 4 months.
Although affected by the outbreak of this year, caused no small impact on the world economy, also inhibits the development of semiconductor industry to a certain extent, but according to the public, according to data from the perspective of a global semiconductor monthly sales figures, the first four months of 2020, the global semiconductor monthly sales remain the trend of the year-on-year growth, 1 - April year-on-year growth of 0.23%, 4.99%, 7.96% and 7.16%, basic return to 2019 levels. According to Chen Jinsong, general manager of Tuofeng Semiconductor, orders for MOS tubes have basically recovered to the same level last year.
According to the latest forecasts from SEMI World Wafer Fab report, it is expected that global wafer fab equipment spending will recover slowly in 2020, with a year-on-year growth of 3 percent to reach $57.8 billion. It is likely to continue to grow in the second half of this year and is expected to reach a record in 2021.
In short, the upstream 8-inch wafer foundry line cannot be started immediately, and many of the wafer production facilities are too old to meet current orders in the short term.
Umc, a leading wafer foundry, said it currently has a monthly capacity of about 80,000 wafers and is producing at full capacity. At present, the monthly production capacity of Leadcore is about 18,000 pieces, approaching full load. Powerchip said it could produce 25, 000 tablets a month by the end of July and was in full capacity and expected to produce 30, 000 by the end of this year.
Upstream foundries are at full capacity and slow production line inputs, which are expected to ease next year. As for the MOS tube market, due to its small profit space, it cannot compete with the power management chip, panel driven IC, etc., or it will transfer the share of shipment to a certain extent, which may lead to a vacancy in the MOS tube market, and the price increase is only the final result.
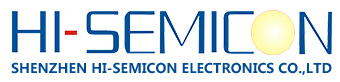